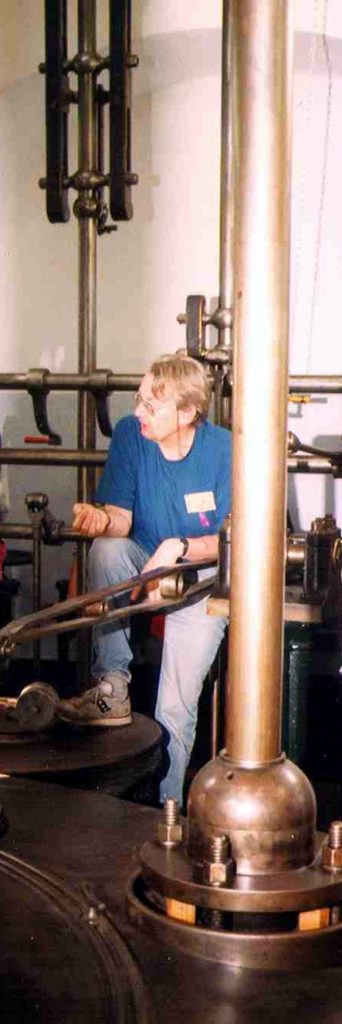
Inleiding
De restauratie was een groot avontuur, het verbazingwekkende verhaal van de StoomPloeg, de vrijwilligers die erin zijn geslaagd de grote Cruquius machine weer tot leven te wekken. Niet met stoomkracht, omdat Cruquius’ ketels gesloopt zijn, maar de oude stoomaandrijving is vervangen door geavanceerde hydraulische techniek. Het volgende verslag van de restauratie werkzaamheden is een fragment uit het `Main engine status report February 2000´ van dr ir Jan A Verbruggen (© copyright Jan A Verbruggen 2000). Jan raakte jaren geleden in de ban van de Cruquius stoommachine én van het weer in beweging stellen ervan. Vanaf dat moment stak hij, samen met andere vrijwilligers, al zijn vrije tijd in de restauratie van deze bijzondere machine. Dit is het verhaal.
Maart 1982
Het Cruquius gemaal werd in 1932 overbodig, de machine stopte haar werk in november van dat jaar. Op 10 juni 1933 werd ze nog een laatste keer opgestookt voor een sluitingsceremonie. In maart 1982 stelde de stichting ` de Cruquius´ een werkgroep in om de mogelijkheid de machine weer in beweging te stellen te onderzoeken. In eerste instantie werden verschillende manieren om de machine aan te drijven vergeleken; men besloot uiteindelijk voor hydraulische aandrijving. Vervolgens werd een aantal aspecten van machine en gebouw onderzocht om na te gaan of deze wel beweging zouden toelaten. In een aantal gevallen hield dit omvangrijke schoonmaakwerkzaamheden en ontmantelingsoperaties in.
Het begon allemaal met `rubbish´
1. Inspectie tunnels
De bouwverordening van 1846 eiste dat de bodem van het machinegebouw geconstrueerd werd in de vorm van een `droge bak´ met bodem en wanden van waterdicht metselwerk. De vloer ligt ongeveer 1 m onder het polderpeil. Op deze 0,5 m dikke vloer ligt het fundament van de centrale machine, met tunnels erin om de onderkant van verschillende ankerbouten te kunnen inspecteren.
In 1983 bleek dat verschillende bodemruimten gevuld waren met `rommel´, voornamelijk dunne zwarte, grijsopdrogende modder. Ongeveer 1 m boven polderniveau ontdekte men een overloopgat in de buitenmuur. De `droge bak´ was kennelijk een waterbassin én een vuilnisvat geworden, waarin alles tot aan de overloop ondergedompeld was in (enigszins bijtende) modder. Als gevolg daarvan was de toegang tot de inspectietunnels geblokkeerd, en zelfs de plaats waar de ingang tot de tunnels zich bevond kon niet meer worden gelokaliseerd.
In 1985 hebben vrijwilligers, emmer voor emmer, ongeveer 10 m3 blubber en rommel moeten verwijderden voordat ze de inspectietunnels weer bloot konden leggen hierbij werden maar weinig voorwerpen gevonden: een klein elliptisch gietijzeren gewicht dat diende om de afvoerkraan van de evenwichtsbuis afgesloten te houden, een wat groter gewicht voor een al lang niet meer gebruikte hefboom van het hydrauliek-kleppensysteem, een moersleutel, een glazen fles, stukken pakking, schoenen…
2. Gewicht
Een inwendig gewichtsoverschot is essentieel voor de werking van het Cruquius type enkelwerkende niet-draaiende machine, en dit blijft zo voor hydraulische aandrijving. Het overwicht moet voldoende zijn om frictie en dergelijke te verhinderen en – omdat besloten is twee van de waterpompen buiten te laten werken – om de benodigde opvoerhoogte te verkrijgen.
Het centrale gewicht, de gewichtsbak, bestaat uit een holle cilindrische hoofdruimte. Het centrale gedeelte is in 6 compartimenten verdeeld. In 4 compartimenten zijn openingen gelaten voor de bevestiging van de balansarmen. De compartimenten werden gevuld met voor dat doel gemaakte gietijzeren gewichten. In later tijden heeft men nog schroot en dergelijke aan de gewichten in de compartimenten toegevoegd.
De netto opvoerkracht benodigd voor 1 pomp is ongeveer 120 kN. Omdat het gewenst was één paar pompen in werking te herstellen, zal de benodigde kracht 250-300 kN zijn, en deze moet geheel geleverd worden door het gewicht.
De totale kracht van de machine (toen deze nog in werking was) is niet nauwkeurig bekend, maar wordt geschat op 600-800 kN. Een verwijdering van 400-500 kN was dus wenselijk. Dit zou bereikt kunnen worden door 40-50 ton inwendig gewicht weg te halen, door eenzelfde hoeveelheid gewicht buiten toe te voegen, of door een combinatie (bijv. verwijder 20-25 ton binnen en voeg de zelfde hoeveelheid buiten toe).
In de loop van 1990 verwijderden vrijwilligers 8440 kg gewicht uit de gewichtskap, deze is nu leeg. Daarna werd nog eens 13555 kg uit de zuigers gehaald. Dit was een veel langzamer, zwaarder en viezer karwei, dat pas begin 1997 werd voltooid. In de ringzuiger (7985 kg) lagen de gewichtsblokken vastgekleefd in een brij van oud, half-vergaan dierlijk vet met water, waaruit ze vrij gemakkelijk losgemaakt konden worden. De blokken in de middenzuiger (5570 kg) echter waren muurvast aan elkaar geroest, verwijderen scheen alleen mogelijk als eerst de roest verwijderd zou worden. Verschillende methoden zijn hiervoor uitgeprobeerd begin jaren 1990, van boren en slijpen tot een heet mengsel van sterk zuur (Blekkenhorst), echter alles zonder resultaat. In 1996 paste Harry Kruk een bruut-geweld methode toe, gebruik makend van de krachtiger gereedschappen die de ploeg toen ter beschikking had. Dit bleek effectief. Het totaal aan verwijderd gewicht is ca 22.2 ton, en als we ongeveer 200 kg aan vet, water en dergelijke toerekenen, resteert er nu ca 40-45 ton inwendig overwicht.
Zo is het avontuur van het restaureren van de grote machine begonnen. De activiteiten bestonden vooral uit schoonmaken, een strijd tegen water, modder en roest, en repareren. Ondertussen werd het denkwerk en voorwerk verricht voor de nieuwe aandrijving.
Aandrijving
Cruquius’ laatste set ketels is ca 1935 gesloopt; alleen sporen van de fundamenten resteren. Het ketelhuis is uiteindelijk in een tentoonstellingszaal veranderd. Om de machine weer in beweging te stellen moest een methode om de machine aan te drijven worden gevonden. Zoals boven al vermeld werden hiervoor verschillende methoden overwogen. Vier alternatieven werden vergeleken: stoom, perslucht, hydraulische en elektrische aandrijving. Elk van deze alternatieven wordt hieronder besproken. Uiteindelijk is gekozen voor moderne minerale olie hydrauliek.
1. Stoom
Dit zou natuurlijk uit historisch oogpunt ideaal zijn, het zou technisch attractief en ook spectaculair zijn. Stoomtoevoer lijkt technisch wel uitvoerbaar, maar andere aspecten als planning en kosten zijn veel problematischer. Het zou de installatie van een fikse stoomvoorziening betekenen, de restauratie van alle machine onderdelen tot volledige staat van werking, en de beschikking over gekwalificeerd (en waarschijnlijk betaald) personeel voor bediening en onderhoud. De kosten (zowel de initiële kosten als de verdere jaarlijkse bedrijfskosten) zouden zeer hoog zijn. Ook zouden er serieuze ruimteproblemen ontstaan: hoe zou een stoomvoorziening gehuisvest kunnen worden zonder een aanzienlijk deel van de ruimte op te offeren, op een manier die zowel vanuit technisch als vanuit het oogpunt van planning acceptabel zou zijn?
Als gevolg hiervan wordt stoomaandrijving niet als haalbaar beschouwd op korte of middellange termijn. Een zeer belangrijk criterium voor welke oplossing dan ook, dient echter te zijn dat deze niet de weg blokkeert van eventuele plannen voor stoomaandrijving in een verder gelegen toekomst.
2. Lucht
Lucht-aandrijving kent soortgelijke toevoer en ruimte problemen als stoom-aandrijving. Een voordeel zou zijn dat een volledig werkende condensor niet noodzakelijk is, maar er zou – net als voor niet-condenserende stoom – wel een een flinke uitlaat gemaakt moeten worden. Afgezien van de condensor zouden, net als voor stoom, alle machine onderdelen hersteld moeten worden tot volledige operationaliteit.
3. Elektrische aandrijving
Elektromechanische aandrijving op een tamelijk centraal punt lijkt niet mogelijk zonder onaanvaardbare beschadiging van de machine (zoals het maken van een groot gat in de bodem van de dubbele cilinder). Een voordeel zou zijn dat machine onderdelen niet volledig werkend en sluitend hoeven te zijn maar slechts beweegbaar.
4. Hydraulische aandrijving
Hydrauliek met standaard onderdelen levert dezelfde voordelen en vraagt minder ruimte dan elektrische aandrijving voor de huidinge aandrijvingsdelen (cilinders), en er is een behoorlijke vrijheid in de keuze van de plaatsing van de krachtbron en de daarmee verbonden onderdelen. Het vinden van een geschikte en niet te opzichtige plek voor de lange aandrijfcilinders levert echter een behoorlijk probleem op. Twee mogelijkheden zijn overwogen.
a. Gebruik een deel van het bestaande passieve hydraulische (buffer) systeem.
Dit subsyteem is aangebracht om schokken als gevolg van ongecontroleerd dichtslaan van de pomzuigerkleppen aan het einde van de stoomslag als het gewicht in de hoogste stand staat te voorkomen. Deze hoogste stand wordt gedurende een afgepaste periode (een paar seconden) `gefixeerd´ om de kleppen de gelegenheid te geven te sluiten. Gedurende de opwaartse (stoom) slag, zuigen twee plunjers van 225 mm (9″) diameter die aan de oren van de gewichtsbak zijn bevestigd water aan uit standpijpen via terugslagkleppen. De waterkolom houdt het gewicht in zijn hoogste stand vast totdat, tegelijk met de machines evenwichtsklep, een klep wordt geopend waardoor het water weer kan wegstromen.
Als dit systeem verbonden zou kunnen worden met een (water) hydraulische krachtbron via extra pijpen op de HP en LP verbindingsleidingen, zou het mogelijk zijn de bestaande plunjers te gebruiken om de machine te bewegen. De plunjers zouden volledig operationeel moeten zijn en alle hydraulische verbindingen en pakkingen zouden dicht moeten zijn. De bestaande kleppen zouden in hun gesloten stand vastgezet moeten worden en behoorlijk dichtgemaakt moeten worden. Door de extra pijpen weer af te sluiten en de bestaande kleppen weer te openen, zou de oorspronkelijke situatie hersteld kunnen worden. Het systeem zou dan weer in originele staat zijn, bijvoorbeeld voor een toekomstig stoomscenario.
b. Richt standaard hydraulische cilinders op `parallel´ aan de buffer plunjers, dus tussen de machine fundering en de oren aan de gewichtsbak, en gebruik standaard minerale olie hydrauliek.
Er is veel energie gestoken in onderzoek naar het water hydrauliek scenario. Uiteindelijk, deels vanwege de voorziene problemen, werd het idee verlaten en ging de voorkeur uit naar minerale olie hydrauliek.
Voor technici, studenten, industriële archeologen, en andere geïnteresseerden, wilt u de complete, engelse, tekst van het status rapport lezen klik hier.