Introduction
The cycle of the Cruquius engine is virtually the same as that of a regular Cornish engine. In nearly all forms of this cycle, steam is used to lift a weight, and then this weight is allowed to descend and operate the pump. For Cruquius the weight is indoors, pushing down on the steam pistons.
Steam cycle
At the start of the stroke, the pistons are at rest in their lowest positions (fig. A). The space above is filled with used steam from the previous stroke. All valves are closed, and there is a vacuum in the condenser and under the annular piston.
1 steam valve
2 equilibrium valve
3 exhaust valve
4 central piston
high pressure HP
5 annular piston
low pressure LP
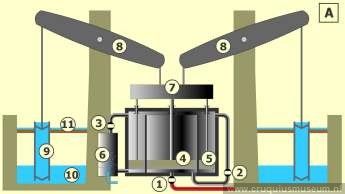
6 condenser
7 crosshead/weight
8 beams
9 pump
10 water in polder
11 collar launder
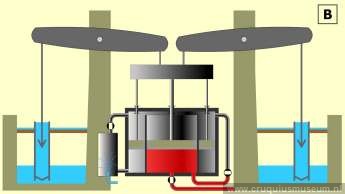
When the exhaust valve and steam valve are opened, the steam above the pistons rushes into the condenser where it is condensed by a spray of water: a vacuum is established above the pistons. Fresh boiler steam is admitted under the HP piston at a pressure of 45 psi, and the pressure differential pushes this piston up, raising the weight and the LP piston, too.
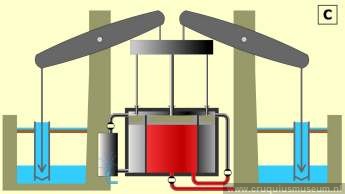
The pump buckets descend, and their clack valves open automatically. The LP piston has vacuum above and below; it is in equilibrium and does not add to the upward push. About halfway up, the steam valve is closed, but the exhaust valve remains open. As the pistons continue to move upwards, the steam under the HP piston expands, so its pressure decreases and so does the upward push. The engine slows down and, if property adjusted, comes to a stop at the top of the stroke, when the exhaust valve is closed.
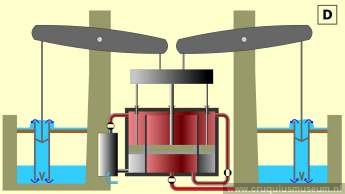
After a brief pause to allow the bucket clacks to close, the equilibrium valve is opened. The partially expanded steam now flows from below the HP piston to the combined space above both pistons. The pistons and the crosshead start to descend by gravity, assisted by the pressure differential over the LP piston. During this stroke, the steam expands further. The pump buckets lift water, while fresh water from the polder enters the pump barrels via the foot valves. At the end of the pump stroke, the equilibrium valve is closed, and the engine comes to a stop in the starting position. After an adjustable pause, the next stroke begins.
Valves and valve gear
A large engine needs large valves, which must open and close quickly to minimize losses. The Cornish engineers developed a double-beat valve which requires only a small lift to open a large passage, and which is almost balanced. So only limited force is needed to open it. The exhaust valve of Cruquius has a diameter of 26″!
Each of the valves is controlled in a similar manner: a lever closes it against the opening force of a weight; and it is held in the closed position by a pawl or ‘scoggan’ which is released at the right moment by a ‘cataract’. An open valve is closed by a clamp on the ‘plug rod’, which moves with the engine. Both the opening and the closing of valves may also be controlled manually, for instance when starting. Various interlocks prevent incorrect combinations of valve positions.
The two pauses mentioned earlier are governed by timing devices named ‘cataracts’. The name is a relic from the earliest form of timer. These used an adjustable trickle of water to gradually fill a vessel which trips when full. The later form of cataract uses a weight-loaded plunger which forces water from a cylinder through an adjustable orifice until a scoggan-catch is tripped. For more information on the valves control go to the valve gear page.
Starting up
After an idle period, the engine cycle described above cannot be started right away. The cylinder is cold, and there is no vacuum in the condenser. The start-up procedure of a large engine like this may take fifteen or twenty minutes. The cylinder is flushed with steam to heat it slowly, and then a number of manually-controlled strokes are made to expel air from the condenser and establish the vacuum. Automatic operation is established only then by activating the cataracts.
The driver of a Cornish engine must always remain vigilant. The stroke length of his engine has to be watched constantly, as it may vary due to small load fluctuations or even the state of lubrication. Frequent small adjustments are required.
The ‘hydraulic’
The large bucket clacks of the pumps are quite slow in closing, and that causes a problem at the top of the stroke. The large mass of the pistons and weight of the engine is pushed up by an elastic cushion of steam, and when it is slowed down, it may oscillate or ‘nod’ a few times before coming to a stop. Such ‘nodding’ of course is transmitted to the pumps. If these move up with the clacks still open, the water flow may cause them to slam shut violently, possibly causing damage.
The solution is to use a column of water to provide a rigid support for the weight until the clacks have closed. Two rams are attached to ears on the weight, and during the upward stroke, these draw water via small non-return valves. This water then supports the weight until, after the required pause, it is released by a valve. The rams, valves, pipes and standpipes together form what is known as the ‘hydraulic’, the use of which in the Haarlemmermeer engines is unique.